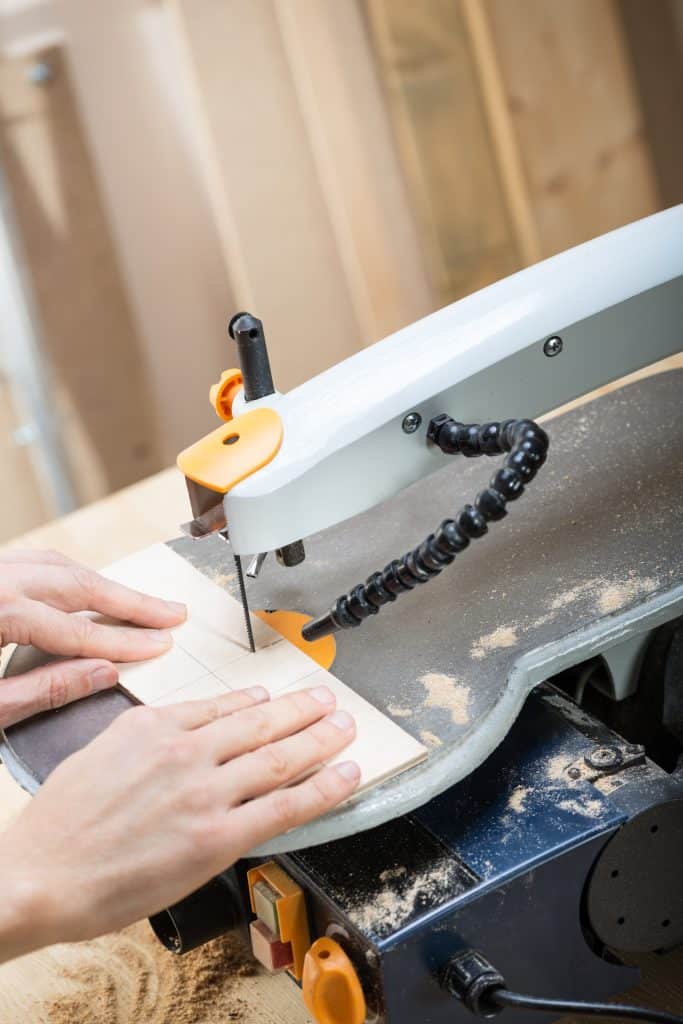
A shadow box made from scroll saws is a great way to display photographs or artwork. A shadow box of small size can give a sense of wonder. A simple scene can be made out of seven layers of 1/4" Baltic birch plywood and measures about four inches square and 1.75 inches thick. Small details add interest and awe to the finished piece. An increase in the size of a shadowbox would require more detail and make it more difficult. The scene in this example is one of the first items on the shadow box's inside.
Shop Fox Classic fence
When building a shadow box with scroll saws, the first thing you should consider is the type and style of fence you will be using. There are several options available, including the T-shape Shop Fox Classic fence, the original fence, and the accessory T-slot fence. Shop Fox Classic fences have a quick-release knife guard and riving blade system. These fences are prewired for use on 120V 20A circuits. They also come with a 10-inch x 40T carbide-tipped knife.
Shop-Fox Classic fence is an option for your next project. This fence is durable and built to last. You have the option to select from a number of patterns including the Five Layer Circle Art Scroll Saw Pattern; the Duck Family Tray Scroll Saw Pattern; the Hanging OrganizerBox; and the Four-Layer Jesus Cross. You can also view the video tutorial for each pattern to help you follow along.
Fox Aluma Classic fence
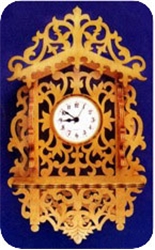
Shop Fox Aluma Classic Fence is a T-shape accessory fencing that fits any shop-made scrollsaw. The fence has the advantage of being easy to adjust, allowing you to cut even the largest panels with ease. The fence can be wired for an ordinary 120V 20A circuit. It also comes equipped with a 10-inch 40T carbide-tipped knife.
Fox Original Fence
The Shop Fox Original fence for scroll saws is an accessory that comes with a T-shape, prewired blade guard and riving knife system. It comes with a riving system and a 10 inch x 40T carbide tipped blade. It's a good idea to start small projects, such as a shadowbox, if your first time scroll sawing.
FAQ
How do you calculate woodworking prices?
It is essential to calculate costs as accurately as possible when pricing any project. Make sure you're getting the best prices on materials. It is important to take into consideration all factors that can impact the cost of your projects. These include time, skill and experience. Check out our guide on the average cost of common DIY projects to get an idea of how much you can spend on woodwork projects.
Do you have any tips on starting a woodworking business?
It takes a lot of effort to start a woodworking business. It's worth it if you're passionate and willing to work hard. You will probably love the challenge of starting your own business.
It is important to remember that unexpected problems may arise when you start a new venture. Unexpectedly, money might run out. You might find customers not willing to pay the amount you expected. You need to be ready for these situations if you want to survive.
Set up a separate account in your bank for your business. You will always know how much money you have coming in.
What kind tools do carpenters use to build?
Carpenters use a hammer as their most common tool. The hammer is used to pound nails into wood. This helps to keep pieces together when they are working on a project. Other tools include clamps. pliers. screwdrivers. measuring tape. pencils. saws. drills. wrenches.
What else should I know about woodworking in general?
It is easy to underestimate how much work it takes to make furniture. Finding the right wood for the project is the hardest part. It can be hard to choose from the many types of wood that are available.
A problem is that wood doesn't have the same properties. Some woods will warp over time, others will split or crack. These factors should be taken into account before buying wood.
How often do I need to buy new supplies
Over time, you may need to replace your tools. Hand tools will need to be sharpened regularly. For power tools, replacement parts will be required frequently. Avoid buying too many products at once. Spread your purchases out over several months.
Statistics
- The U.S. Bureau of Labor Statistics (BLS) estimates that the number of jobs for woodworkers will decline by 4% between 2019 and 2029. (indeed.com)
- The best-paid 10 percent make $76,000, while the lowest-paid 10 percent make $34,000. (zippia.com)
- Overall employment of woodworkers is projected to grow 8 percent from 2020 to 2030, about as fast as the average for all occupations. (bls.gov)
- In 2014, there were just over 237,000 jobs for all woodworkers, with other wood product manufacturing employing 23 percent; wood kitchen cabinets and countertop manufacturing employing 21 percent. (theartcareerproject.com)
External Links
How To
How to join wood with no nails
Woodworking is a favorite hobby. Woodworking is a relaxing hobby that allows you to use your hands to create useful things from wood. Sometimes you may want to join two pieces together of wood without using nails. This article will teach you how to do this to keep your woodwork projects looking great.
Before you can join the wood pieces together, you need to remove any rough edges. Sharp corners can cause problems down the line. Once you've done this, you're ready to start gluing your boards together.
When working with hardwood, glue should be applied only to one side. You should glue both sides if you are working with softwoods such as pine and cedar. Once the glue has dried, press the boards together until they are fully adhered. Before you proceed to the next step, be sure to let the glue dry completely.
After you've glued your boards, you'll want to drill holes into the joints where you plan to insert screws. Depending on the type of screw that you use, the size of these holes will vary. For example, if your screw is a 1/2-inch wooden screw, drill a hole that is at minimum 3/4 inches deep.
After drilling the holes, you can drive the screws into your board's backside. Do not hit the boards' front surfaces. It will ruin the finish. Don't drive the screws too far into the end. This will help prevent splitting of the end grain.
Once your project is complete, it's time to protect it against the elements. You have two options: seal the whole furniture piece or just the top. You'll want a product that lasts for many years. Some examples include oil-based varnishes, polyurethane, shellac, lacquer, etc.
These products are available at most home improvement stores. It is important to ensure that you purchase the correct product for the job. Some finishes are toxic and should not ever be used indoors. When handling certain finishes, wear protective gear.